This article is a guide for making Chainmail Armor from start (simple wire) to finish (a finished chainmail shirt). We will be using the European 4 in 1 weave, as this is the most common weave. This is the weave that you usually see in movies.
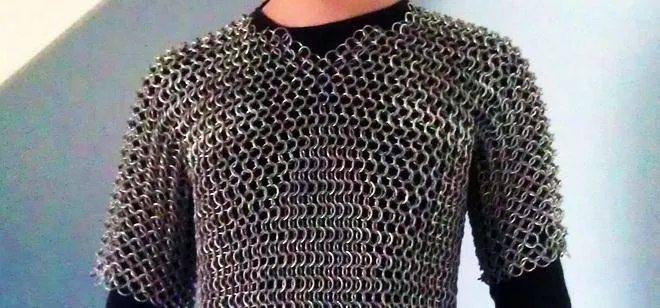
There are several sections to this guide: Materials, Making the Rings, Weaving the Rings, and Making the shirt.
There are two ways to go about making chainmail armor. The cheaper but more time consuming method is to make the rings yourself. The quicker, but more expensive way is to order the metal rings online from a site such as The Ring Lord. If you choose to get your rings pre-made, then you can skip the second section of this guide, "Making the Rings." Whichever method you choose, I hope you enjoy this guide.
If you have any questions, ask in the comments section and I will try my best to answer them!
Also, at the end of the guide, I have a few alternate ideas for making chainmail. Check them out!
Materials
The basic materials you need are two pliers and rings. If you are making your own rings you will need additional materials, but I will cover that further down in the guide. However, there are many points to consider when considering what to use.
First we have the wire (or ring). Here are several points to consider while choosing.
Step 1: Choosing the Metal
The metal that the rings will be made from is one of the factors that will determine how strong the armor is in the end. It also determines how expensive and difficult your project will be. The weaker and more pliable the wire is, the weaker the armor will be because the rings will break easier. Also, the weaker and more pliable the wire is, the easier the rings will be to open and close. Generally, this makes the wire cheaper as well, but not in all cases. Here are the pros and cons of several common Chain Mail metals.
- Aluminum: Aluminum wire is extremely cheap (I made a chain vest with only thirty five dollars out of Aluminum) but very weak as well. Aluminum gives a very shiny, silver look when cleaned. You can also get Anodized Aluminum, which comes in many brilliant colors. If you are looking to make costume armor or chain jewelry that does not need to be strong, then this is a good choice because this metal is very light.
- Steel: Steel is generally a happy medium for those who want strength and affordability. You can get Mild, Galvanized, or Stainless steel. Mild steel is strong but has the problem of rusting if not properly cared for. It also has a dull appearance and gives a medieval look. Galvanized steel is cheaper, reasonably strong, but dirty, and it is the most common chainmail metal. Stainless steel is my personal favorite metal for making armor. It is reasonably cheap and very strong and shiny. Plus, it's clean and rust proof. You can buy this with a black magnatite coating if you want a different look. This metal is about 3x heavier than aluminum, a good choice for Functional Armor. Expect a shirt to weight over 10 pounds.
- Brass, Copper, and Bronze: These metals give a penny like appearance and are rather strong. They are all expensive; however, copper is especially expensive. They are all very corrosion resistant, making them another good choice for Functional Armor. These metals are also quite heavy.
- Titanium: Titanium is very strong. It is a wonderful metal for armor. It can be bought in variious colors as well. The pros to this metal is that it has almost unparralelled strength and will make super armor. The cons are that it is rather expensive and difficult to bend. This Metal is also pretty light.
- Gold and silver: These metals are extrordinarily expensive and very weak. Obviously, these are not a good choice for armor, but they do make very nice jewelry, although they are ather heavy.
Step 2: Choosing the Gauge
The gauge of the armor is a measurement of how thin the wire or rings are. When wire was made hundreds of years ago, the metal would be put through a gauge machine over and over. The more times it went through, the more fine it became. This measurement is still in use. The higher the gauge, the thinner and weaker the wire. In general, anything 16 gauge and lower is quality armor. 18 to 20 works but is weaker. Anything 22 or higher is very thin and really only good for costume strength chainmail and jewelry. The higher the gauge, the less expensive the wire becomes.
Step 3: Choosing the Size of Ring.
Choose the size (diameter) of ring you want for your armor. Obviously, the smaller the the diameter of the rings, the longer it will take because you will need to connect more rings together and the more expensive it becomes because your armor will be more dense. However, the smaller the diameter of the ring the stronger the armor is. Don't get this confused with Gauge; when I say a smaller ring, I mean a smaller diameter of ring, not a thinner ring. I've made Chain Mail shirts with both 3/16 and 5/16 inch ring sizes. These are both good sizes. This is one way to compensate for having weaker metal. By using more rings, you improve the strength.
Tips
- I am currently making a shirt with 5/16 inch, 16 gauge, spring temper stainless steel rings. This shirt is very strong. If you want a nice, cool looking, strong shirt, these are good specs.
- Check out theringlord.com for more information on the individual metals. They also include armor ratings for each of the individual gauges and metals. Even if you don't buy from them, this is a good resource to get more information.
Warnings
- If you are making costume strength armor and plan to use a high gauge and weak metal, make sure it is strong enough to hold its own weight. Other wise the shoulders might start opening due to the shirt's own weight dragging it down.
Step 4: Choosing Pliers
You need to have two pliers at minimum to actually weave the Chainmail. I prefer to use medium size, flat nose, craftsman pliers with no teeth at the tip. Teeth aren't really a problem except they scratch the rings and start to bend out of shape due to the heavy usage you will be putting them through. But don't feel that you need to buy brand new tools for this project; really, any old pliers will do.
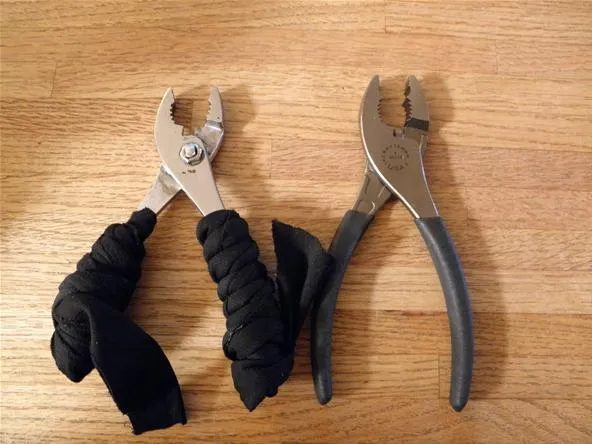
Tips
- If you are going to buy pliers, Craftsman pliers are a good choice because all craftsman tools have a lifetime warranty. So if you ever break them from heavy usage, then just get them replaced for free!
- If you are using lower gauges and stronger metal then the rings will be difficult to bend open and closed. After a while this can start to hurt your hands because of all the pressure put on them. I like to get some lengths of soft cloth, any old material will do, and wrap them around the pliers' handles to make them more padded and comfortable.
- Some Mailers like to use a pair of needle nose pliers to help thread the rings together. This becomes necessary if you use a very tight weave with small rings.
Warnings
- If you are making armor for a group like SCA, or LARP or AMPGARD or any such roleplaying group, check with the people in charge before you buy your supplies. Many times they have specifications on how thick the gauge must be, or what kinds of metal it has to be made of. It is always a drag to spend countless hours making a shirt only to find out that it doesn't fit the qualifications and can't be used. This has happened to me. So be sure to check!
Step 5: Making Rings
If you plan to make your own rings from wire, then progress to the next section and I will cover how to do this and what materials you need. If you already have your rings all set, then carry on to the third section, "Weaving the Rings."
Making the Rings
This section will teach you to make rings from wire. The basic idea is to wrap the wire around a metal rod, making a coil. One then cuts the coil down the length to make rings of wire. However, this gets very difficult if you do it by hand. I have found a simple set up that is very easy to create that really speeds up the process.
Step 6: Get the Materials
These are the materials you need for creating and operating the set up.
- an 18 inch, 1 by 4, piece of wood. (The Base)
- two, 4 inch, 2 by 4, pieces of wood. (The ends)
- a 24 inch, Metal Rod with a diameter equal to the size of ring you want. (The Core)
- a power drill. (The Engine to turn the core)
- a drill bit with a diameter slightly larger than the diameter of the metal rod.
- a drill bit with a diameter just slightly larger than the wire you plan to use. In other words, If you made a hole with this drill bit, the wire should be able to be threaded through.
- the wire you plan to use to make the rings out of.
- a work glove to protect your hand.
- a C Clamp to hold the set up down whilst in operation.
- several nails or screws.
- wire cutters (If you have a low gauge or a very hard metal, Such as titanium or steel, you will need heavier duty wire cutters). Again, I recommend getting Craftsman wire cutters because of the life time warranty. These cutters will be cutting every ring, so you may have to replace them after a while.
Step 7: Building the Set Up
- Take the drill bit with the diameter slightly larger than the metal rod and use it to drill a hole completely through one of the 4 inch, 2 by 4's. The hole should be nearer to one end than the other.
- Take the same drill bit and drill a hole in the same place as the other, except only half way through the block this time.
- Attach the 4 inch, 2 by 4's on either end of the 18 inch, 1 by 4. They should be set up so that the holes you just drilled are facing each other. This will form a "[" laying on its back. Make sure the holes are directly across from each other, so that the metal rod could go through one and into the other.
- This step is a little tricky. You need to take the smaller drill bit, the one whose diameter is just big enough to fit the wire through, and drill a hole through the metal rod. This will be difficult. The bit will have a habit of slipping off the round edge. One way to help is to etch a notch on the round edge of the rod with a nail first. The placement of this is important. Put the rod through the hole in the first block and into the half hole in the second. Put the hole in the rod near one of the blocks IN BETWEEN the blocks. This will take a long time to drill through. Have patience.
- Put the rod through the first block and into the second.
- Apply the C clamp to the the base, attaching it to the table.
Here is a picture of the set up without the Rod.
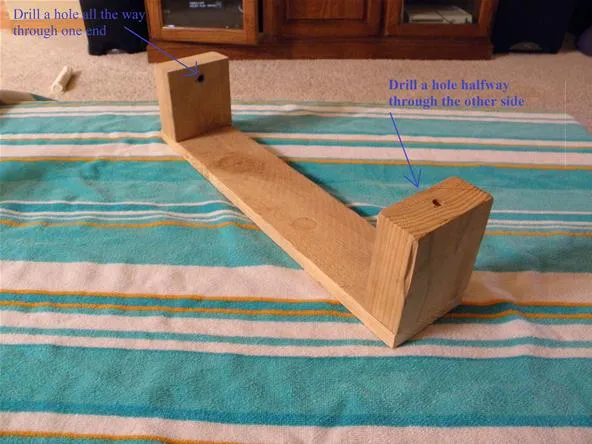
Here is a Picture of the set up completed.
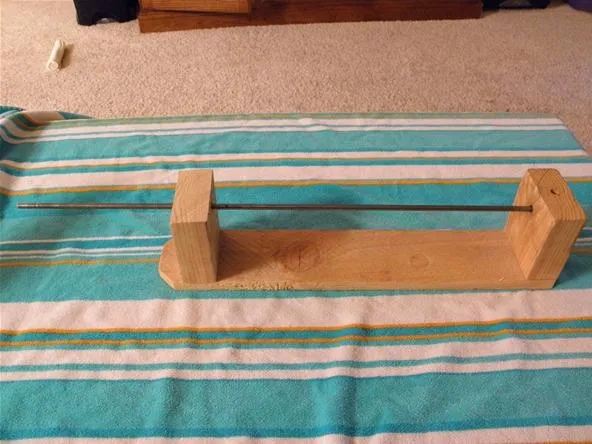
Here is a picture with the hole in the rod.

Step 8: Operating the Set Up
- Open tip of the drill (the place you put the bits in) and put the end of the rod in. Then tighten it. This will allow you to use the drill to spin the rod.
- Thread the end of your wire into the hole in the metal rod.
- Put on the glove and hold the wire with it.
- Use your other hand to operate the drill. Spin the rod and guide the wire so that it coils around the rod.
- Once the entire rod has wire coiled around it, cut the wire. Now cut the other end that went through the hole, and pull the rod out of the contraption.
- Take the coils of the rod, and start to cut them down the length. You now have rings to start making your chain mail!
The set up in action.
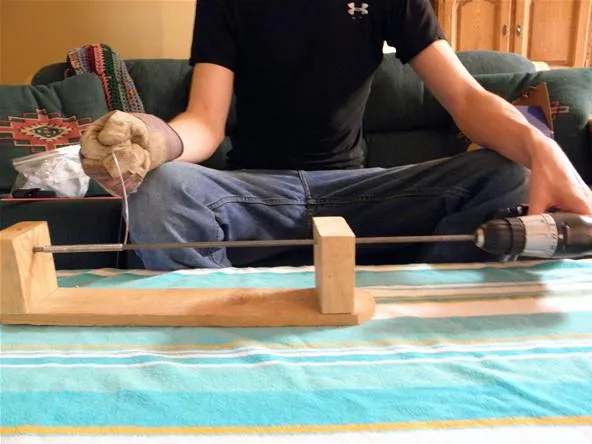
Close up.
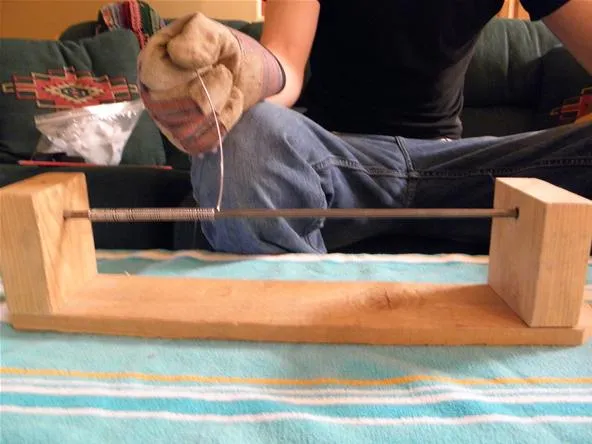
Closer.
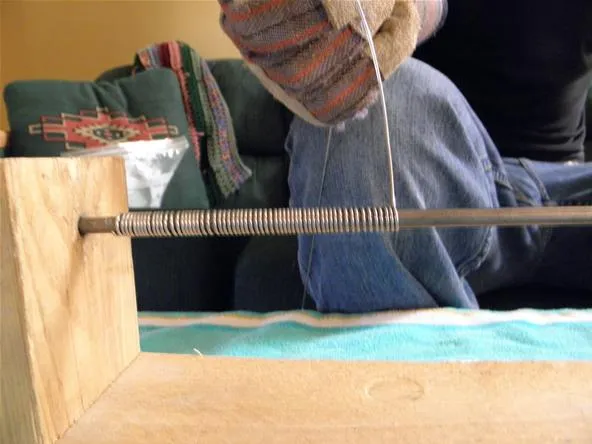
Cut the end you inserted into the hole to take the coil off
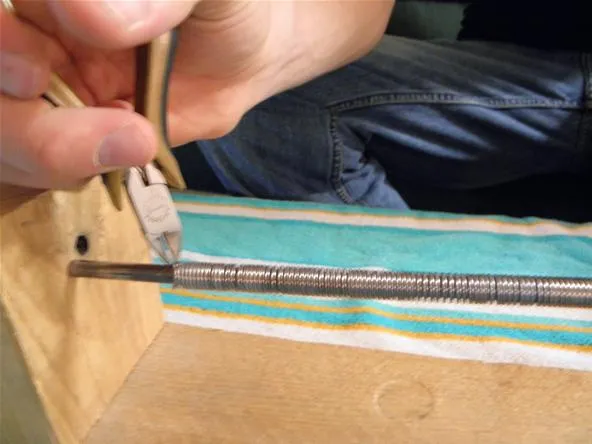
Cut the rings off down the length of the coil and start making chain mail!
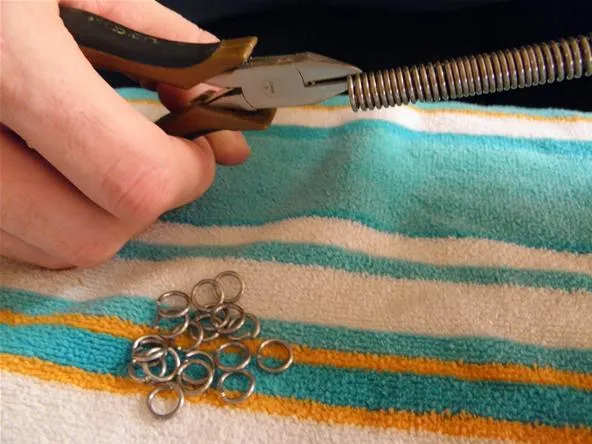
Warnings
- Be warned, if you are making a shirt or a hauburk, you will need a lot of rings. You will need any where from 5,000-20,000 rings depending on the ring size, weave, and type of shirt. This process will take a long time and a lot of patience!
Weaving the Rings
As I said before, we will be using the European 4 in 1 weave. The weave is called this because it was developed and used in Europe and because every one ring is attached to 4 other rings. This weave is not very difficult. If you want to do other weaves, I will try to upload more how to's for them in the future.
Step 9: Closing the Rings
About half the rings you use will need to be closed before adding them to the weave. To do this, simply take your two pliers and bend the ends of the rings together. If you want to make quality armor that looks nice and functions well, you need to make sure that the ends of the rings are flush. This means that there should not be any empty space between the ends and that the rings should not feel jagged if you run your finger around the ring. You may have to use the pliers to squeeze the ends past each other before you close them.
Step 10: Making Open Rings
By the nature of the rings, when you bend them closed or open, the ends will start to drift apart. As about half the rings you use will be closed, half of them will need to be open to fit into the weave. This means that you are going to have to use the pliers to squeeze the ends of the ring past each other.
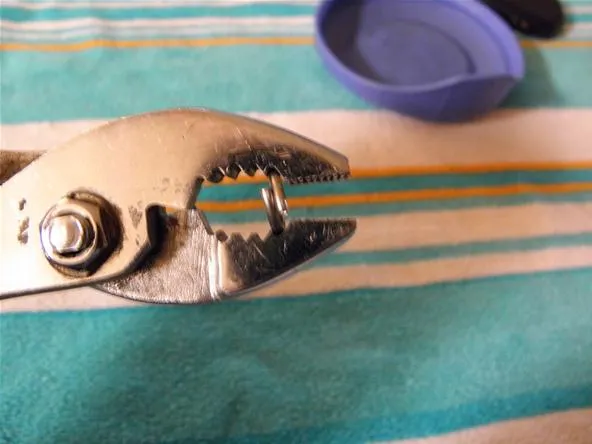
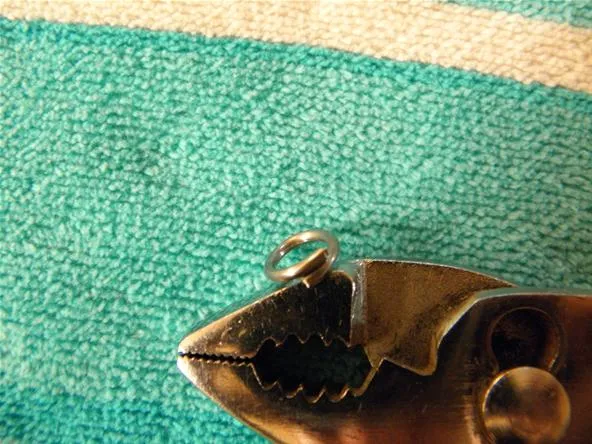
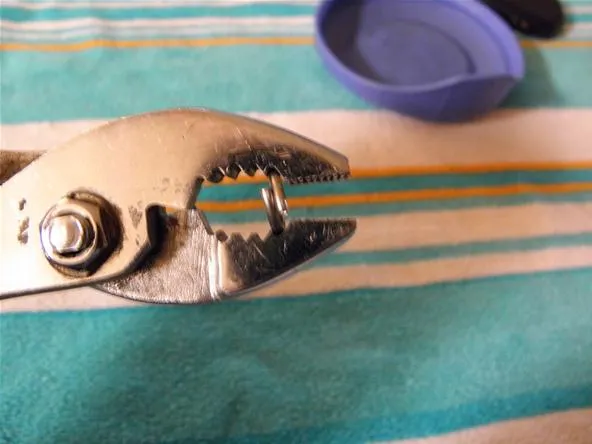
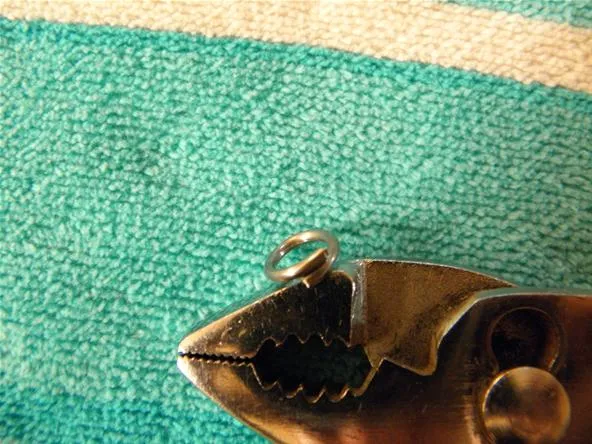
Step 11: Making Sets of Five
Now you will take one of the "Open Rings" (The ones from step 10) and thread four "Closed Rings" onto the ring you just opened. Now close that ring. You should have four rings attached to one ring. Do this several times.
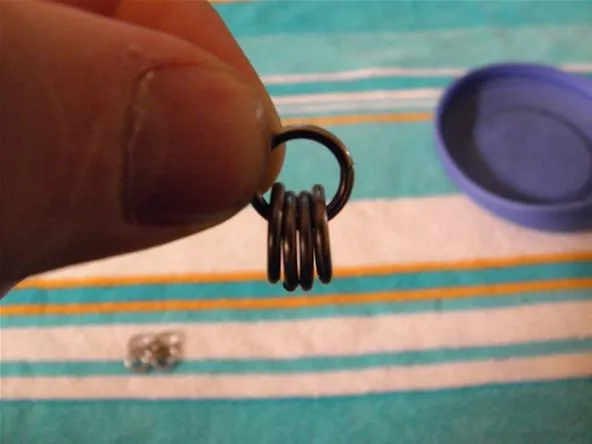
Step 12: Connecting the Sets of Five into Strands
Take two of your Sets of Five and lay them out in such a way that the original "Open Ring" is in the middle of the four "Closed Rings." There should be two "Closed Rings" on each side of the "Open Ring." See the picture for more detail.
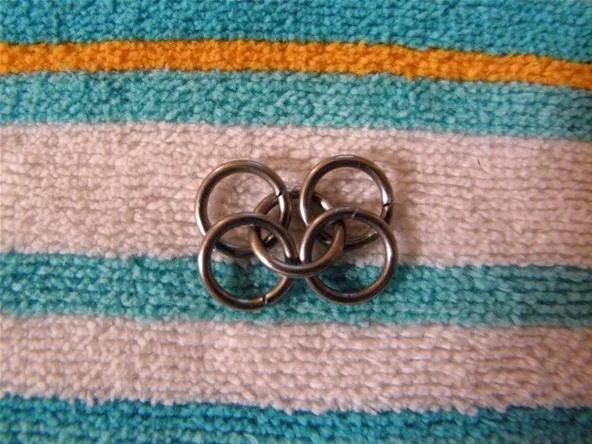
Now lay them on top of each other like such.
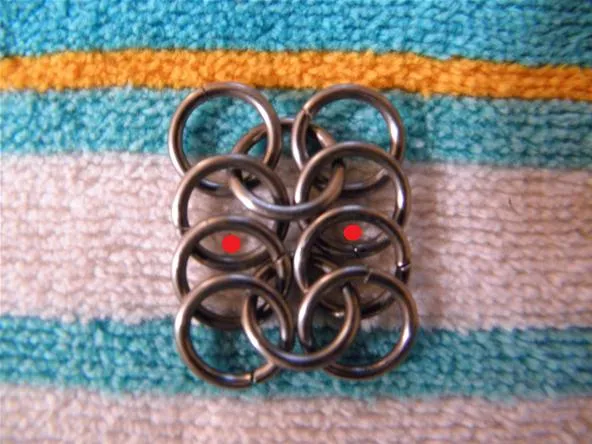
Now, you have to open another ring. Thread the ring through the spaces where those little red dots are.
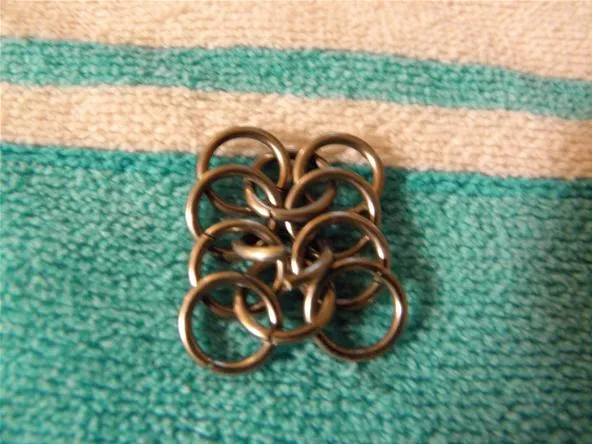
Close the ring. Do this several more times with more sets of five. It will look like this.
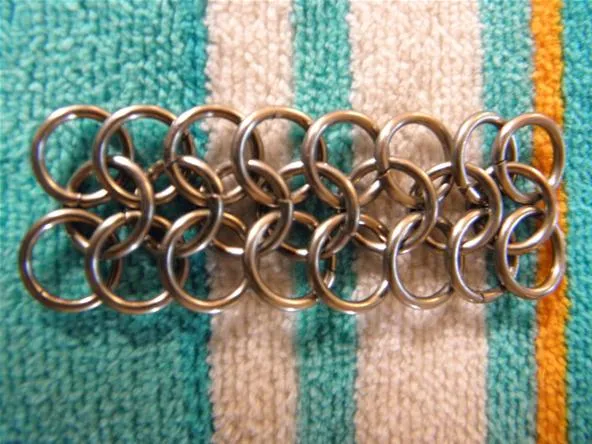
Make this strand long enough to completely encircle your chest with a chest full of air.
Step 13: Connecting the Strands
Now, lay two strands next to each other. Take an open ring, and thread it through the overlaps on the edges (where the red dots are), connecting them together. Do this all the way up the strand. It should look like this.
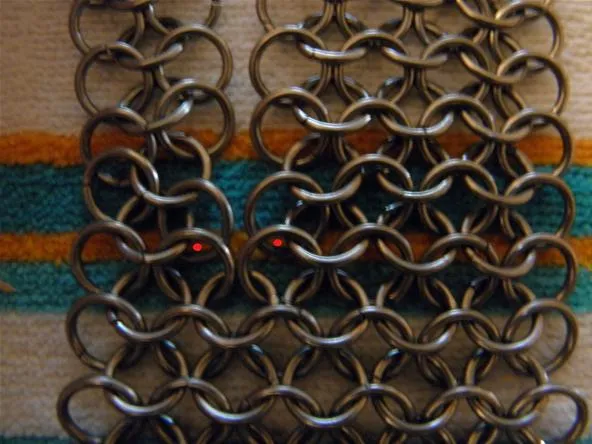

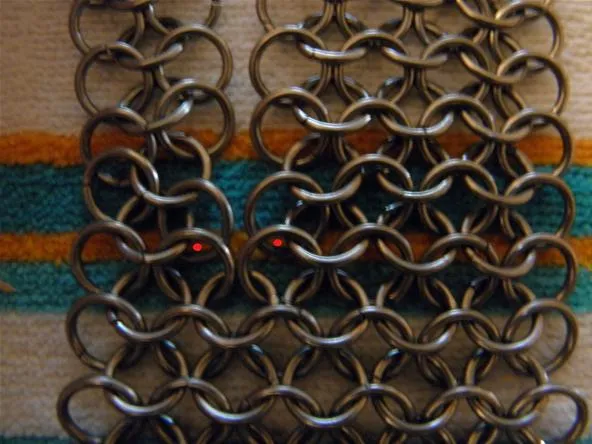

You have now made a section of chain mail!!! Congrats! Now, to fashion the shirt!
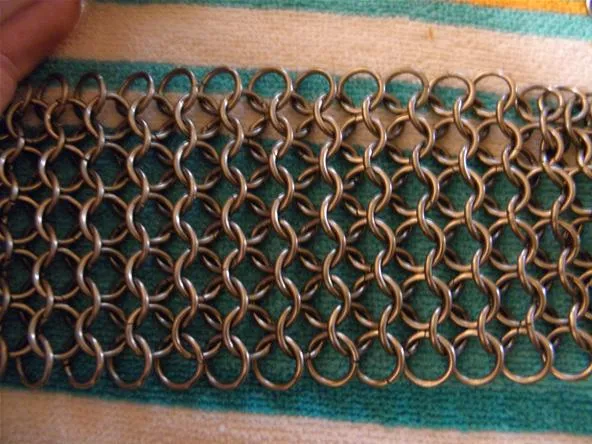
Making the Shirt
This section is very simple.
Step 14: Armpit to Waist
I usually start by making many more of those strands (the ones that can encircle your chest) and connect them together, until you get enough chain material to go from just under your armpit to your waist, or however far you decide to go. Next, simply connect the ends together to form a tube.
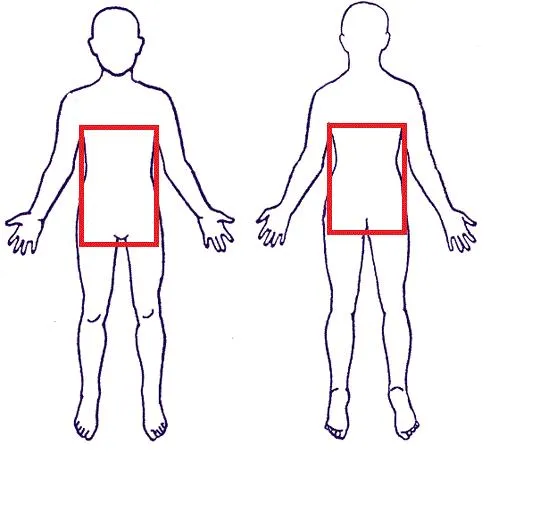
Warnings
- You can make the Chainmail larger around in some places and smaller in others, by simply making varying lengths of strands and skipping links as you attach them. It may seem like a good idea to do this and make a shirt that fits perfectly to your body, but, Chainmail, unlike cloth, does not stretch. So every part must be able to get over your shoulders, with your hands straight up in the air. In most cases, if it is never smaller than needed to encircle your chest with a full breath of air, you will be able to squeeze into it. It is a good idea to test this though. Put your arms in the air above you head, and get some one to try and wrap it around your shoulders. If it comes together, then you should be fine. How ever, if you have wide hips or a large belly and would like it to be more form fitting, you can use this technique to make the bottom larger. But again, the shape of the tube must be conical, or you won't be able to get it on.
Step 15: Shoulder Straps
Make two straps that will go over the shoulders and hold it up. It will look like overalls.
Make sure that you make the rings go in the same direction; otherwise, it won't connect, and that's no fun.
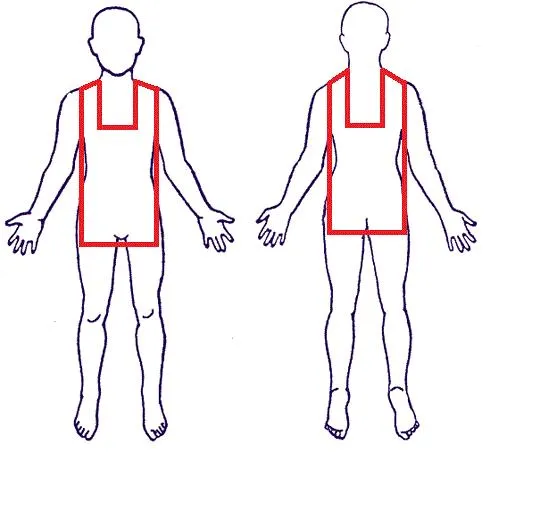
Step 16: Neck
This section is a little tedious. You are going make the upper back and the upper chest. Once you put in the sections for the upper back and upper chest, you are going to want to add in rings, one at a time, to make it look neat and well crafted.
Warnings
- Make sure the Neck hole will go over your head. For obvious reasons.
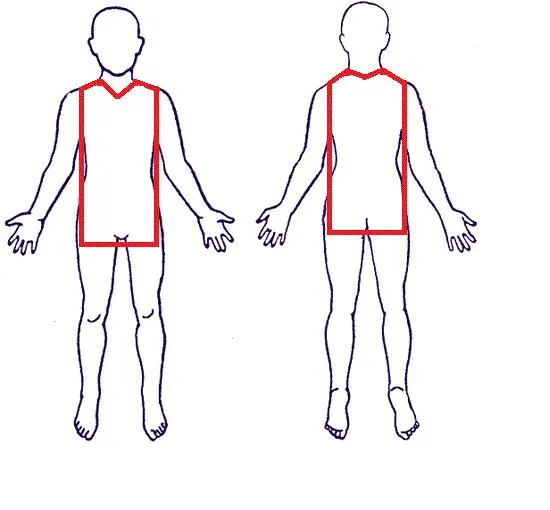
You can stop here and skip to step 19. You have a very fine chain mail vest done! If you chose to make sleeves, then continue on.
Step 17: Sleeves
For sleeves, simply make tubes that can encase your arm. Make sure the rings go in the same direction as the vest so the sleeve and vest will connect. However, don't expect the arm pit on the sleeve to connect to the armpit on the vest - they won't connect because the rings will be going in different directions. This is unavoidable. Many people leave the armpit unconnected. Other people connect it as best they can. It keeps it functional but it doesn't look the best. The choice is really up to you. Do what ever you like the best!
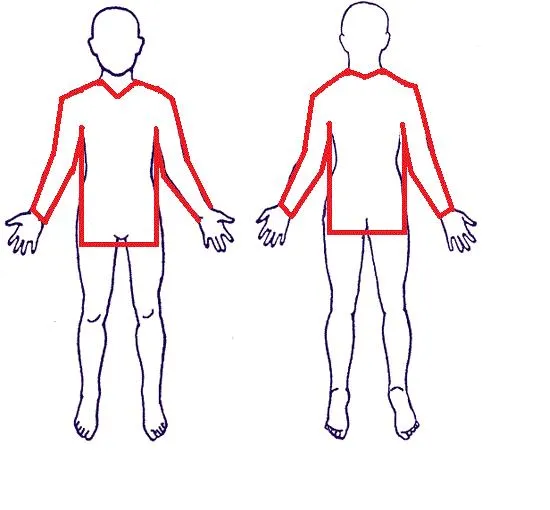
Step 18: Skirt
If you are happy with the shirt, then stop and skip ahead to step 19. If you want to make a full suit, then make the skirt.
This is easy. Make two sections of chain material that would each be half of a tube the same size as the armpit to waist tube we made at the beginning of this section. It should generally be long enough to go to mid thigh or to the knee, but this is completely up to you again. The length is just whatever you like the best.
Next, you attach it to the bottom of the shirt in the exact same way as you would if you were just extending the shirt's length. Do not connect the edges together, though. The reason for this is so that you can open and close your legs whilst still protecting your flank. If you connect them, you'll look like a mermaid.... which would be weird, but hey, what ever floats your boat :)
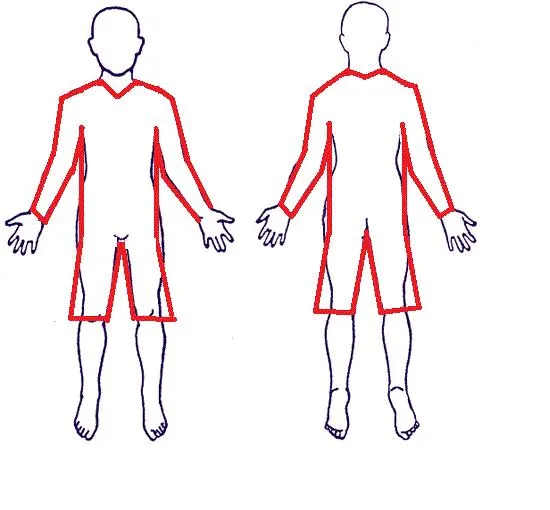
Step 19: Wash It
Generally if you give your Chain Mail a good wash it will come out shinier, especially if you use a dirty metal like mild steel or aluminum. A normal washing machine does a good job buy it might hurt your machine as it will be a rather heavy piece of metal.
Step 20: Put It On!
Put on your Chain Mail! Go to a mirror and admire your handiwork! You put a hell of a lot of time into this, and probably grew a few gray hairs. But you did it! Go out and show it off! Annoy all your friends! Have a party in its honor! Congratulations!
Tips
- If you would like to make a form fitting shirt or vest, make it like a corset. Leave the back open and but in some laces. This will give the armor a definite feminine look however. Be warned.
- You could punch holes in some metal plates and attach them with segments. This would make a nice variation.
- Use different colors in the same shirt to make designs or just make it seem varied.
- If you have any cool ideas or pictures of chain mail projects you have done, post them in the comments and help spread inspiration to our fellow maillers!
Thank you all very much for reading my Guide to Making Chain Mail Armor- From Start to Finish on wonderhowto.com. If you have any questions, just ask away in the comment section or send me a message. Again, Thank you and happy Mailling!
Comments
No Comments Exist
Be the first, drop a comment!